Case Study: How a Batangas Refinery Cut Downtime by 62%
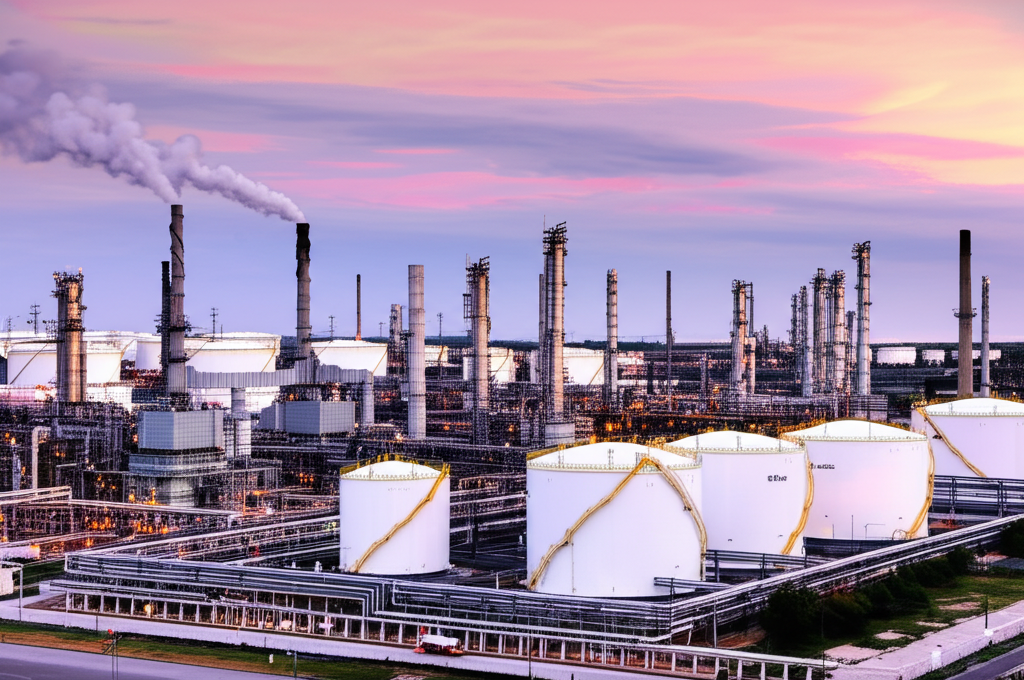
A major petroleum refinery in Batangas faced recurring challenges with heat exchanger cleaning during scheduled turnarounds. Traditional cleaning methods required extensive confined space entry, manual labor, and extended downtime—directly impacting production capacity and revenue.
The Challenge
The refinery's 24 shell-and-tube heat exchangers required cleaning every 18-24 months, with each cleaning operation taking 3-5 days per unit. This translated to:
- 72-120 days of cumulative cleaning time
- Significant confined space entry risks
- Inconsistent cleaning results affecting thermal efficiency
- Production losses estimated at ₱2.8M per day
The Solution
Dezu implemented a comprehensive solution centered around automated tube cleaning technology:
- Custom-designed robotic tube cleaning system with flexible lance
- Programmed motion control systems for cleaning patterns based on fouling analysis
- Remote operation capabilities eliminating confined space entry
- Real-time cleaning verification through flow testing
The Results
After implementing the automated solution, the refinery experienced transformative results:
- 62% reduction in overall cleaning time (from 3-5 days to 1-2 days per exchanger)
- 100% elimination of confined space entry requirements
- 15% improvement in post-cleaning thermal efficiency
- Standardized cleaning quality regardless of operator experience
- ROI achieved within the first turnaround cycle
The success of this implementation has led to the refinery adopting similar automated approaches for other maintenance operations, creating a roadmap for digital transformation of their maintenance practices.