Systems Thinking: Why Most Maintenance Programs Fail
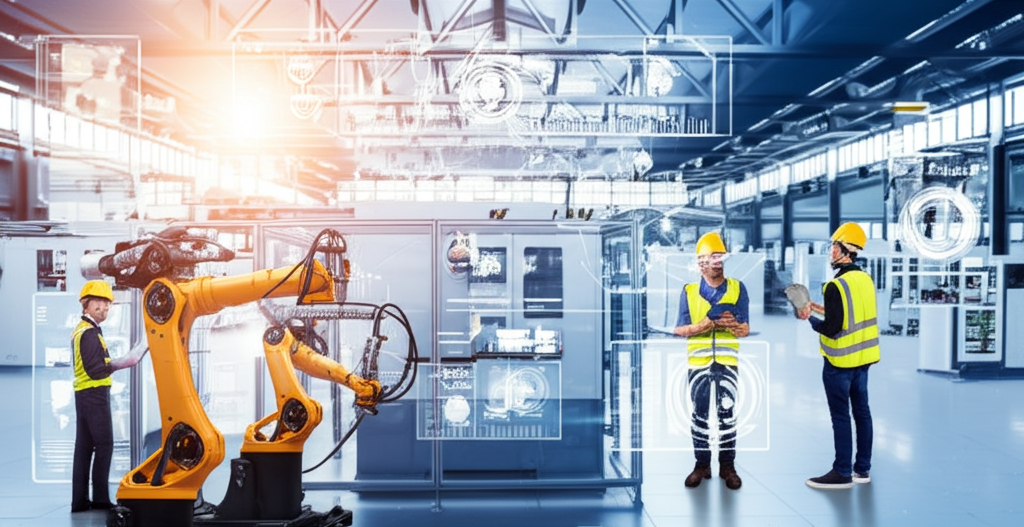
Despite significant investments in maintenance programs, equipment, and training, many industrial operations still struggle with recurring failures, unexpected downtime, and maintenance backlogs. The missing element is often systems thinking—understanding how components interact rather than focusing on isolated parts.
The Maintenance Iceberg
Visible maintenance activities—repairs, replacements, and scheduled downtime—represent only 20% of what determines maintenance success. Below the surface lie the interconnected factors that truly drive outcomes:
- Information flows between operations and maintenance
- Incentive structures and performance metrics
- Tool and parts availability systems
- Knowledge transfer mechanisms
- Decision-making hierarchies
Common Failure Patterns
Our analysis of maintenance programs across 35 industrial facilities in the Philippines revealed three common systemic failure patterns:
1. The Firefighting Trap
When reactive work exceeds 30% of maintenance activities, teams become trapped in a cycle where urgent repairs prevent proactive work, creating more failures and more reactive work.
2. The Data-Action Disconnect
Many operations collect maintenance data but lack the systems to convert insights into specific actions, creating "data-rich but insight-poor" environments.
3. The Capability-Responsibility Gap
Maintenance teams are often held responsible for outcomes they lack the authority, resources, or capabilities to influence—creating systemic frustration and workarounds.
Systems-Based Solutions
Effective maintenance programs require interventions at the systems level:
- Redesigning information flows to connect operations and maintenance
- Creating shared metrics that align incentives across departments
- Implementing decision-making frameworks that balance short and long-term priorities
- Developing feedback loops that capture and apply learning
The most successful maintenance transformations we've observed start not with new equipment or procedures, but with mapping the current system to identify leverage points where small changes can produce outsized results.