Waterjet vs. Traditional Methods: A Cost Analysis
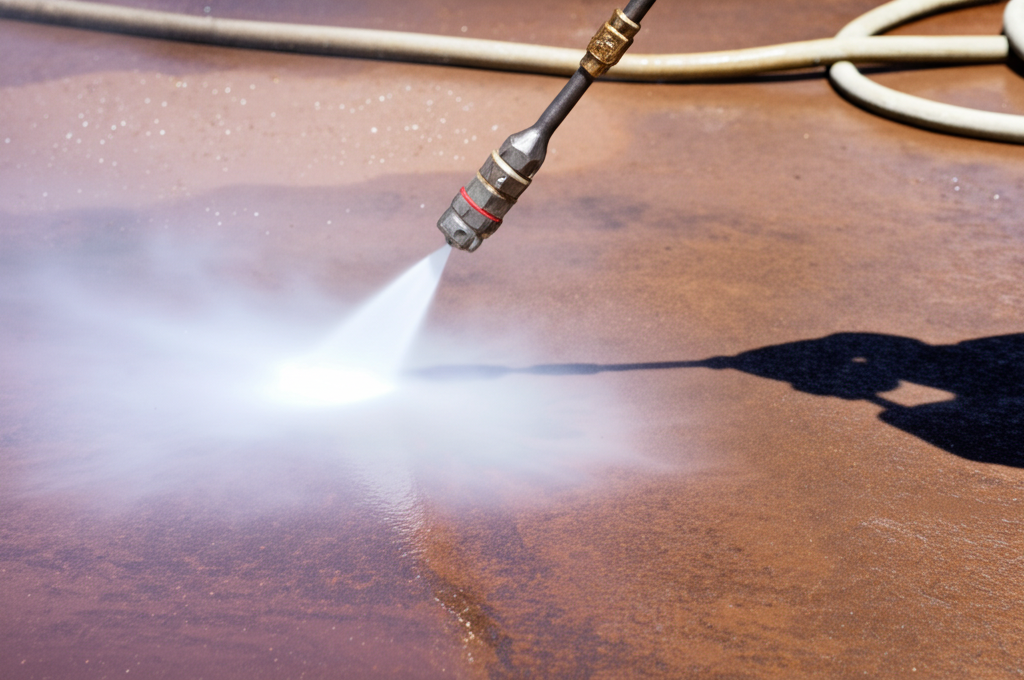
When evaluating cleaning and surface preparation methods, the initial equipment cost often overshadows the total operational picture. This analysis breaks down the true cost comparison between waterjet technology and traditional methods like chemical cleaning, manual scraping, and abrasive blasting.
Initial Investment: Beyond the Equipment
While waterjet systems typically require a higher upfront investment, the total first-year costs tell a different story when you factor in:
- Consumables and chemical costs
- Personal protective equipment requirements
- Training and certification
- Environmental compliance measures
Operational Efficiency: Time is Money
Our field tests across 12 industrial sites in the Philippines showed that waterjet cleaning completed tasks 40-60% faster than traditional methods, with even greater advantages in complex geometries and confined spaces.
Hidden Costs of Traditional Methods
Traditional cleaning approaches carry significant hidden costs that rarely appear in initial estimates:
- Extended downtime during cleaning operations
- Secondary cleaning to remove chemical residues
- Waste disposal and environmental compliance
- Surface damage requiring additional repairs
The Five-Year Picture
When projected over a five-year operational period, waterjet technology demonstrated a 32% lower total cost of ownership compared to traditional methods, with the break-even point typically occurring between 14-18 months after implementation.
For operations considering the transition to waterjet technology, the key is matching the right pressure and flow specifications to your specific application—overspecifying equipment is one of the most common causes of poor ROI in waterjet implementations.