The Future of Robotics in Philippine Manufacturing
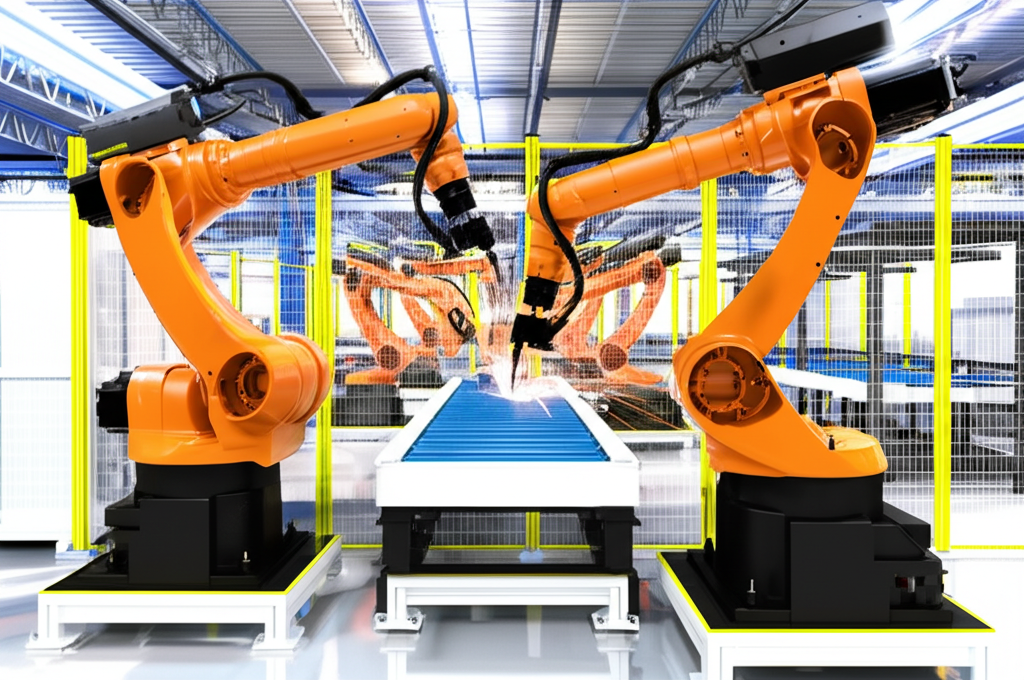
The global manufacturing landscape is being reshaped by robotics and automation, with the Philippines at a critical inflection point. While the country has traditionally relied on labor cost advantages, the narrowing gap between human and robotic labor costs is forcing a strategic rethinking across industries.
Current State: Pockets of Excellence
Robotics adoption in Philippine manufacturing currently exists in pockets of excellence rather than widespread implementation:
- Semiconductor and electronics: High adoption rates comparable to global standards
- Automotive components: Moderate adoption focused on repetitive tasks
- Food processing: Early-stage adoption primarily in packaging
- Heavy industry: Limited adoption with significant potential
Emerging Trends
Our research with manufacturing leaders across the country reveals five key trends shaping the future:
1. Collaborative Robotics
Rather than full automation, Philippine manufacturers are increasingly deploying collaborative robots that work alongside humans, augmenting rather than replacing labor.
2. Modular and Flexible Systems
Given the diverse production requirements of many Philippine operations, robotics systems that can be quickly reconfigured for different products are gaining traction.
3. Domestic Innovation Ecosystem
A growing network of local robotics integrators, software developers, and maintenance specialists is reducing the barriers to adoption and support.
4. Skills Transformation
Technical schools and universities are rapidly developing robotics-focused curricula to address the emerging skills gap.
5. Robotics-as-a-Service
Subscription and pay-per-use models are making robotics accessible to SMEs that previously couldn't justify the capital investment.
The Path Forward
For Philippine manufacturers, the robotics journey requires a staged approach:
- Process standardization and documentation
- Targeted automation of high-value processes
- Workforce development in parallel with technology deployment
- Integration of robotics into broader digital transformation initiatives
The most successful implementations we've observed start not with technology selection, but with clear identification of the specific operational challenges robotics can address.